About us
KLEIBERIT Adhesives – The Specialist Amongst Adhesive Manufacturers. KLEIBERIT adhesives are an now integral part of the world we live in. Today KLEIBERIT SE & Co. KG is based in Weingarten Baden (Southern Germany) and also has one of the most modern and innovative research and production centres worldwide. Innovative adhesive systems for a wide field of applications are being developed in cooperation with, and produced for international customers. The product range is designed specifically for customer requirements and worldwide availability is ensured with an intelligent logistics concept.

© thodonal - stock.adobe.com
New ideas develop together with customers
Adhesive bonding is the bonding technology of the future. KLEIBERIT’S strategy is to continue to provide new innovations for a wide field of applications. One investment for the future is the shown by the opening of the TECHNICAL CENTER in 2009. Customer can regularly be found here working closely with KLEIBERIT engineers and technical personnel to develop specific product solutions.
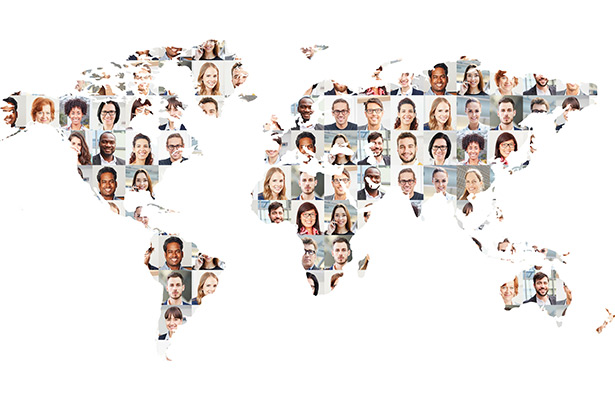
© Robert Kneschke - stock.adobe.com
KLEIBERIT Adhesives employs approximately 700 people worldwide.
Shareholder Dipl. Physicis Klaus Becker-Weimann, places value on high qualification in all areas, from purchasing and development to production, from quality management to delivery and customer consultation.
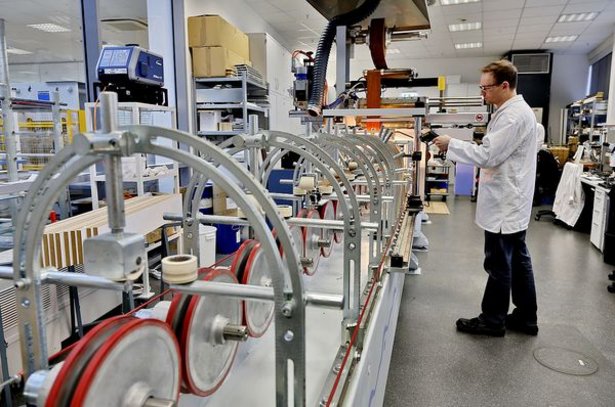
© Mirko Bartels
Research and development secure the future
The KLEIBERIT trademark stands for innovative research and development, the most modern production, highest product quality as well as service oriented, customer focused and competent consultation. And this for 75 years.
In the last 25 years, KLEIBERIT has become a global trendsetter for PUR adhesive systems and has significantly influenced the market with its innovative product ideas.
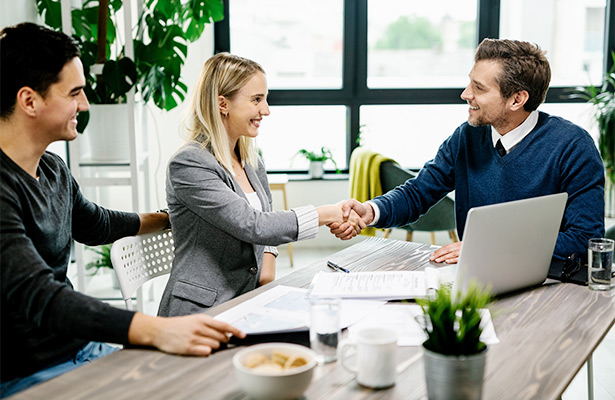
© Drazen - stock.adobe.com
Every customer is number one with us.
With our worldwide network of Sales Engineers, and our presence in all markets worldwide, we provide our customers solutions and offers which are designed to meet their specific demands. Almost every national language is spoken within our on-site Sales Administration and Customer Consultation Centre in Weingarten. By working closely with machine and material manufacturers, we offer practical and innovative adhesive systems which meet a wide variety of international standards and norms. An intelligent logistics concept with a modern fully automated high rack warehouse ensures product availability at the right time at the right place.
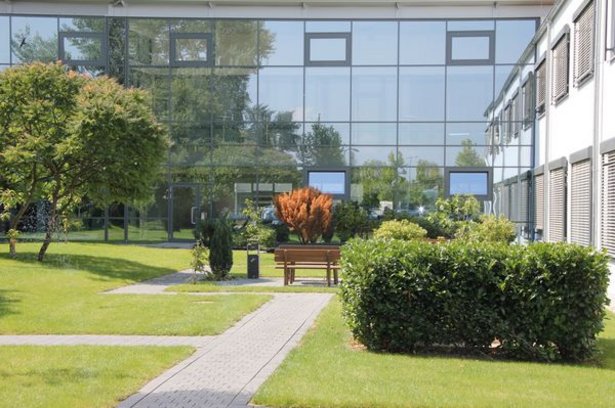
© KLEIBERIT
We live the principle of sustainability in processes and procedures according to certified quality and environmental management
Responsibility towards the environment and the people in research, development, production and logistics is one of the main goals at KLEIBERIT. Our demand to combine high product quality with environmental and health and safety of the workforce accompanies our innovation process from the beginning. We also want to further develop this global responsibility in the future with sustainable processes and goals.
Corporate Compliance Policy incl. Modern Slavery Act
HK Holz- und Kunststoffverarbeitung Supplement SURFACE-MAGAZIN (2021)
Autor: Reinhard Huber
Global success story
KLEIBERIT HotCoating® succeeds in what other wet coatings cannot - successfully coating untreated melamine.
What initially began as a polyurethane hotmelt adhesive applied via roller coater, is today an international patented process by KLEBCHEMIE M. G. Becker GmbH & Co. KG, located in Weingarten, Germany – commercially known as KLEIBERIT – that influences surface trends across the world, penetrates established markets and is even used for outdoor applications.
Sustained success has encouraged the family-run SME to increase production capacities by an expected 60,000 tons within the next three years, thus doubling KLEIBERIT’s current capacity. CEO Leonhard Ritzhaupt announced this to our editorial office in the run-up to the virtual Ligna 2021 trade fair, adding that investments in further HotCoating production plants are in the pipeline for that reason. “This is a clear commitment to Germany as a business location,” says Peter Mansky, head of Marketing and Communications.
The talks with the managers in Weingarten revealed a wide range of factors that have enabled and promoted this development.
Alongside the excellent product characteristics, what really stands out is the KLEIBERIT team’s ability to cooperate strategically with external partners such as Spanish machine manufacturer Barberan. This distinctly sets the company apart from other technology providers and is an increasingly important aspect in times of progressive digitalization of processes and systems.
Full package comprising patented process + demo line Rainer Kampwerth (Sales Manager HotCoating and Industrial Coatings) and Jens Fandrey (Technical Manager HotCoating and Surface Technologies) know that, in addition to the strong partnerships with machine manufacturers, a significant part of the success is due to its subsidiary, dekoraPUR GmbH located in Barsinghausen/ Hanover, Germany (see various DRW publications, e.g. MDF & Co. Magazine 2016).
A complete HotCoating line was installed there at an early stage for coating furniture components, e.g. for kitchen manufacturers, and lately also for coating edges. In Barsinghausen, the KLEIBERIT team has unrestricted access to an industrial line operating under real production conditions, where new and further developments, sample parts, customer trainings, and technology tests can be conducted at any time.
What a dream for every application engineer, developer or salesperson. Who else has that kind of almost permanent access?
KLEIBERIT thus manages to offer a complete package that is surely unique – an internationally patented process with strong references, a demo line under own control, and customer trainings in real conditions including the use of customers own material.
The dekoraPUR line, equipped for a wide range of different applications, provides a significant competitive advantage. Time-tomarket is a key issue nowadays. Risk minimization, fast developments, persuasiveness, and creating acceptance and trust are just a few of the positive effects that KLEIBERIT, as well as its partners and customers, benefit from.
Successful examples can be found worldwide, for instance, at Kastamonu, PG Bison, Duratex, and Tafisa – all significant players in their respective markets. Pfleiderer’s Primeboard (see Surface Magazine 2017/ Laminat Magazine 2018) also originated there.
History and development of KLEIBERIT HotCoating® technology
It all began in the flooring market, says Jens Fandrey, specifically with the Swiss company Lico’s cork flooring. The adhesion quality on the digitally printed cork substrate, the permanent elasticity and surface durability (with its high, AC5-rated abrasion resistance) soon convinced the renowned manufacturer and, subsequently, the related market.
HotCoating’s hybrid structure comprises two layers: polyurethane in micro-emission quality for coating, and a compatible UV acrylic lacquer as a top coat. The reactive PUR layer bonds with moisture, protects the surface and digital prints, and the acrylic top coat layer hardens upon UV radiation. Furniture manufacturers also benefit from these features.
They wanted more added value, higher quality and product personalization of decorative as well as digitally printed boards.
Demand from the industry was for such surfaces to be finished with high-gloss and super matt coating, and to provide optimal adhesion between the melamine surface and the lacquer coat. Conventional coating systems showed problems with adhesion to the melamine. High investments were made in equipment and expensive primers were used as bonding agents, applied to surfaces that had been finely sanded several times. But high reject rates on account of adhesive problems upon further processing failed to convince the manufacturers and the market.
Just how HotCoating manages to achieve high adhesion levels without the use of a primer remains a well-kept secret. The HotCoating layer forms a composite unit with the melamine surface, the digital printing and the top coat, and also meets all the other requirements of the panel industry.
Even subsequent pore embossing up to 150mμ with existing short-cycle presses will not cause any cracking in the lacquer. The crucial factors for success and high market acceptance are the special properties in subsequent processing; one such example being Pfleiderer’s Primeboard.
In times of invisible glue lines and laser edges, it is essential that sawing doesn’t cause any chips or jaggedness on or along the edges or on the surface layer. This is the only way to ensure that the edge banding is flush without any visible seams. Any chips in the top layer would lead to a very expensive reject. In production lines set up for mass customization, any reworking requirements have an impact on productivity. Not to mention the current price increases of board material, which also have to be factored in.
One solution follows the next challeng
The compact panel for exterior use was one such challenge. The tolerant HotCoating even allows rework on site, even with less ideal tools. The demonstrated robustness in practical application and resistance to water, cold, heat as well as UV light impresses customers.
Market feedback far exceeds KLEIBERIT's cautious expectations.
Coating thin and pliable HPL was also an obvious choice, according to Fandrey. The pliability and flexibility of the coating layer was a core requirement, especially for CPL.
Further processing, for example in the postforming process, requires the ability to process very tight radii down to 2-3 mm. Not every lacquer or coating can cope with this, at least not without forming fine hairline cracks. HotCoating has also succeeded here, as the successful application at Stylam Industries/India clearly shows.
Further innovations in sight
From the outside, the intensive relationship of all those involved with the core technology convinces even the last doubter. Every advance, every new application brings experience and knowledge that is actively shared within the KLEIBERIT team. In this way, it is always possible to jointly open up new fields that previously seemed impossible and that bring new motivation and success, according to Mansky.
Only in this way is it possible to realize topics such as inert curing for high gloss or excimer technology for the production of super-matt, almost reflection-free surfaces. The clear functional structure of the HotCoating layer, the deep understanding of the experts involved, the additional experience of the partner companies involved, the openness and willingness to share the knowledge gained in order to subsequently find new solutions is the secret of success at KLEIBERIT, of this the author is convinced.
What could be more obvious than to open further new chapters with roll-to-roll coating as well. At LIGNA 2017, KLEIBERIT demonstrated live the first system with inline digital printing.
A masterstroke in the eyes of the experts. Jens Fandrey and Rainer Kampwerth proudly report on the current large roll-to-roll installation in Florida/USA. A service provider for coating printed papers and thermoplastic films, has invested in a 1600 mm wide HotCoating line from machine partner HUSER.
KLEIBERIT also supports this customer with the complete package from the inquiry to the commissioning. Even after commissioning, the customer benefits from the strong partnership and the innovative drive from Weingarten.
2009 The first industrial unit for coating flooring elements goes into operation at Lico, Switzerland
2012 Operations begin at the first industrial unit for high-gloss coating of wood-based boards at Kastamonu in Istanbul, Turkey
2018 Operations begin at the first industrial unit for coating digitally printed fibre cement-based flooring boards
2018 Operations begin at the high-gloss and super matt coating unit at Pfleiderer in Leutkirch, Germany
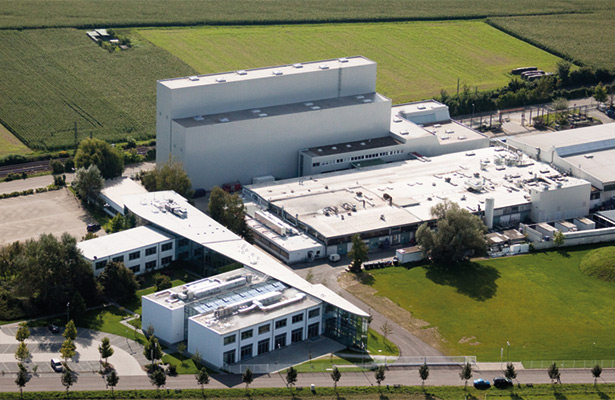
© 2009 Werner Riehm: www.FLY-FOTO.de
The customer provides our direction.
KLEIBERIT is geared towards effective communication with customers and a horizontal company structure makes this possible.
There are three business areas: Sales to the wood processing trade via distributors with a corresponding customer service representative. Industrial sales domestically and abroad, both inside and outside of Europe, with an engineering consultancy network directly on-site. External consultants are supported by internal personnel in Weingarten as well as by subsidiaries or branch offices in the primary sales regions.
Production is exclusively in Weingarten.
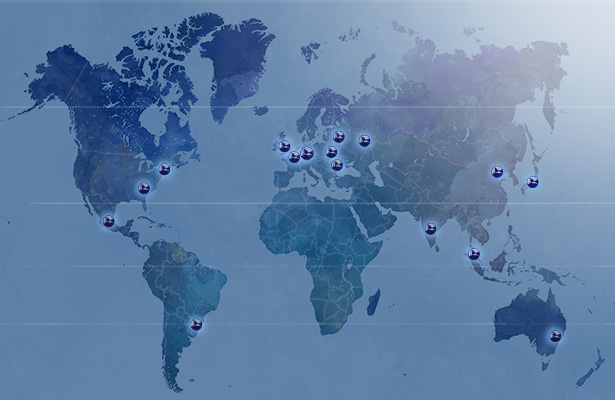
The success of KLEIBERIT is a global success
Customers all over the world trust us and count on our quality and service. For this reason KLEIBERIT is represented with sales offices in the most important areas of the world.