Über uns
KLEIBERIT Klebstoffe - Der Spezialist unter den Klebstoffherstellern. KLEIBERIT Klebstoffe sind aus vielen Bereichen unserer modernen Welt nicht mehr wegzudenken. Heute ist KLEIBERIT SE & Co. KG, im badischen Weingarten gelegen, eines der modernsten und innovativsten Forschungs- und Fertigungszentren weltweit. Hier werden im engen Dialog mit den internationalen Kunden innovative Klebstoffsysteme entwickelt und produziert, die in vielen Bereichen Anwendung finden. Das Produktportfolio ist exakt auf die Bedürfnisse der Kunden abgestimmt und die weltweite Verfügbarkeit durch ein intelligentes Logistikkonzept gesichert.
Innovationen

© thodonal - stock.adobe.com
Im Dialog mit den Kunden entstehen neue Ideen
Kleben ist die Verbindungstechnologie des neuen Jahrtausends. Die Strategie des Unternehmens setzt auch weiterhin auf Innovationen in vielen Anwendungsbereichen. Die Investition in die Zukunft zeigt sich in der Neueröffnung des KLEIBERIT Technologiezentrums im Jahr 2009. Hier sind die Kunden regelmäßig zu Gast, um im Dialog mit den KLEIBERIT Ingenieuren und Technikern spezifische Produktlösungen zu erarbeiten.
Mitarbeitende
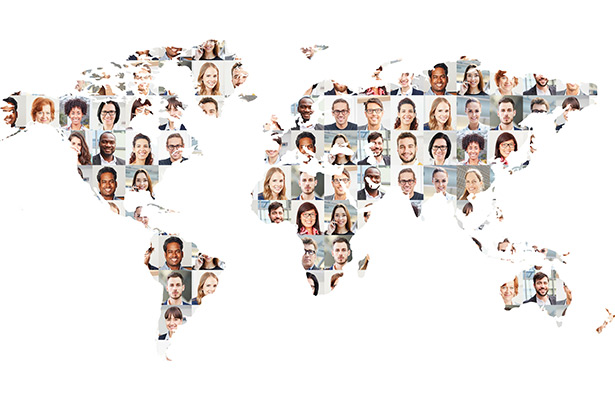
© Robert Kneschke - stock.adobe.com
KLEIBERIT Klebstoffe beschäftigt weltweit 700 Menschen
Gesellschafter Dipl. Physiker Klaus Becker-Weimann legt Wert auf allergrößte Qualifikation in allen Bereichen, von der Entwicklung, Beschaffung über die Fertigung, vom Qualitätsmanagement bis zur Auslieferung und der Beratung beim Kunden.
Competence PUR
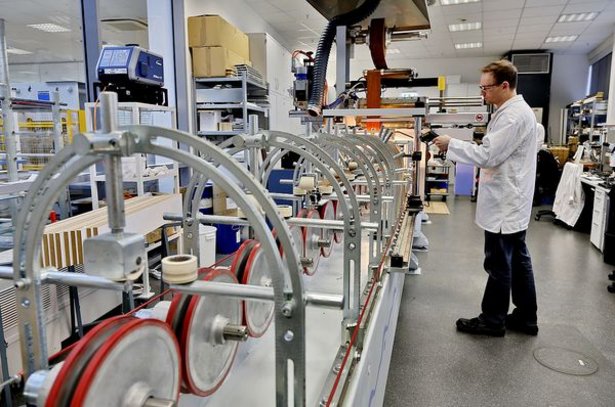
© Mirko Bartels
Forschung und Entwicklung sichern die Zukunft
Die Marke KLEIBERIT steht für innovative Forschung und Entwicklung, für modernste Fertigung, höchste Produktqualität sowie für serviceorientierte Kundennähe und kompe- tente Beratung. Und dies seit 75 Jahren.
In den letzten 25 Jahren hat sich KLEIBERIT zum globalen Trendsetter im Bereich reaktiver PUR-Klebstoffsysteme entwickelt und hat mit seinen innovativen Produktideen den Markt nachhaltig beeinflusst.
Kundenzufriedenheit
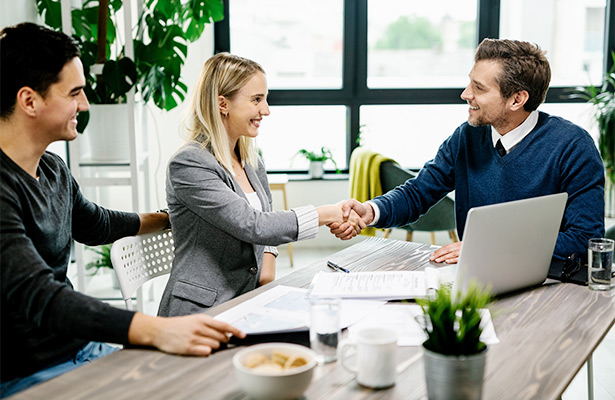
© Drazen - stock.adobe.com
Bei uns ist jeder Kunde die Nummer Eins
In vielen Märkten und allen Regionen dieser Welt unterwegs, sprechen wir fast jede Landessprache und sind über ein flächendeckendes Service- und Beratungsnetz direkt vor Ort. In Zusammenarbeit mit namhaften Material- und Maschinenherstellern bieten wir Gesamtlösungen nach internationalen Standards und Normen.
Gesellschaftliche Verantwortung
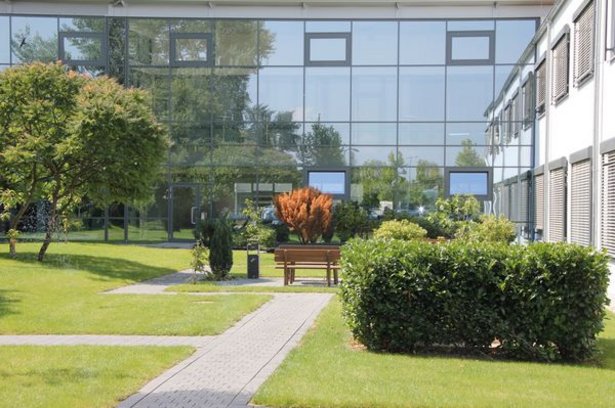
© KLEIBERIT
Wir leben das Prinzip der Nachhaltigkeit in Prozessen und Abläufen nach zertifiziertem Qualitäts- und Umweltmanagement
Verantwortung gegenüber der Umwelt und den Menschen in Forschung, Entwicklung, Produktion und Logistik ist eines der Hauptziele bei KLEIBERIT. Unser Anspruch, hohe Produktqualität mit wirksamem Umwelt- und Arbeitsschutz zu verknüpfen, begleitet unsere Innovationsprozesse von Beginn an. Auch in Zukunft wollen wir diese globale Verantwortung mit nachhaltigen Prozessen und Zielen weiterentwickeln.
Hier können Sie unsere Corporate Compliance Policy herunterladen
Chronik
1948 Gründung der Firma in Ebenhausen bei Ingolstadt durch die Gesellschafter Dipl.-Chem. Max Becker, Dr. Werner Klingele, Dr. Heinz Otto
1960 Verlagerung des Unternehmens nach Baden-Württemberg in das neu errichtete Werk in Weingarten
1965 Beginn der Produktion von Kanten-SK
1966 Erweiterung des Werkes um 1.000 m²
1976 Erweiterung des Werkes um 900 m²
1980 Erweiterung des Bürotraktes
1981 Gründung von KLEIBERIT Frankreich
1990 Hochregallager mit 2.250 Stellplätzen
1991 Verkaufsbüro Moskau
1992 Verkaufsbüro England
1996 Gründung der KLEIBERIT-Töchter in Kanada und USA
1998 Unterwasser-Granulator für SK-Produktion, Neubau Rohstoffhalle mit 2.300 m²
1998 Verkaufsbüro Süd-Ost-Asien
1999 Verkaufsbüro Australien
2000 Neue Ummantelungsanlage für das KLEIBERIT Technikum
2001 3-Tonnen-Mischer für PUR-SK Tanklager für Polyole (PUR-SK Produktion) Deltapac-Abfüllanlage
2001 Neubau Verwaltungsgebäude
2002 Gründung KLEIBERIT Adhesives of Japan
2008 Zweites Hochregallager mit 6.500 Stellplätzen
2008 Gründung KLEIBERIT China
2008 Gründung KLEIBERIT Russland
2009 Technologiezentrum, Weingarten
2012 Gründung KLEIBERIT Adhesives India Pvt. Ltd.
2012 Gründung KLEIBERIT Ukraine
2012 Verkaufsbüro KLEBCHEMIE Weißrussland
2012 Gründung KLEIBERIT Kimya San. ve Tic. A.Ş., Türkei
2012 Gründung KLEIBERIT do Brasil Comércio de Adesivos e Vernizes Ltda.
2013 Gründung KLEIBERIT Bel, Weißrussland
2014 Gründung KLEIBERIT Adhesives México S.A. de C.V., Mexiko
2016 Gründung KLEIBERIT AUSTRALIA Pty Ltd.
2018 Gründung KLEIBERIT Coatings Asia Pte. Ltd.
2023 Umfirmierung in KLEIBERIT SE & Co. KG
HK Holz- und Kunststoffverarbeitung Supplement SURFACE-MAGAZIN (2021)
Autor: Reinhard Huber
Globale Erfolgsspur
KLEIBERIT HotCoating® gelingt, was andere Nass-Beschichtungen nicht können - unbehandeltes Melamin erfolgreich zu lackieren.
Was als heiß aufgewalzter Polyurethan-Schmelzklebstoff begann, ist heute ein international patentiertes Verfahren von KLEIBERIT, das weltweit die Oberflächentrends beeinflusst, in etablierte Lack-Märkte eindringt und selbst in Outdoor Anwendungen zum Einsatz kommt.
Der bisherige Erfolg überzeugte das familiengeführte, mittelständische Unternehmen so sehr, dass Geschäftsführer Leonhard Ritzhaupt uns beim traditionellen Redaktionsgespräch zur Vorbereitung der virtuellen Ligna 2021, eine Verdoppelung der KLEIBERIT-Produktionskapazitäten um 60.000 Tonnen innerhalb der nächsten 3 Jahre ankündigt. Hierbei wird u. a. auch in weitere Anlagen zur HotCoating-Produktion investiert. „Ein klares Bekenntnis zum Standort Deutschland“, so Peter Mansky, verantwortlich für Marketing und Kommunikation.
Die Diskussion mit den verantwortlichen Managern in Weingarten zeigt einen ganzen Strauß an Faktoren, die diese Entwicklung ermöglichten und beeinflussten.
Neben den herausragenden Produkteigenschaften ist, nach Ansicht des Autors, besonders die Fähigkeit des KLEIBERIT-Teams zur strategischen Kooperation mit externen Partnern, wie z. B. dem spanischen Maschinenhersteller Barberan, hervor zu heben. Sicherlich ein deutliches Zeichen, welches den Unterschied zu anderen Technologieanbietern markiert. Im Übrigen eine Eigenschaft, die man auch in Zeiten fortschreitender Digitalisierung in den Prozessen und Systemen mehr und mehr anerkennt, so der Autor.
Für Rainer Kampwerth (Vertriebsleiter für HotCoating und Industrielacke) sowie Jens Fandrey (Technischer Leiter für HotCoating und Oberflächentechnik) hängt der Erfolg, neben den starken Partnerschaften zum Maschinenbau, besonders auch an der Schwesterfirma DekoraPUR in Barsinghausen/Hannover. Hier wurde bereits frühzeitig eine komplette HotCoating-Linie installiert, auf welcher Möbelelemente für z. B. Küchenhersteller beschichtet und neuerdings auch mit Kanten konfektioniert werden können.
Dort steht dem KLEIBERIT-Team jederzeit eine industrielle Anlage im realen Produktionsbetrieb zur Verfügung, auf der Neu- und Weiterentwicklungen, Musterteile, Kunden-Trainings oder Technologietests ohne Verzögerung durchgeführt werden können.
Ein Traum für jeden Anwendungstechniker, Entwickler oder Verkäufer. Fast jederzeit zugänglich. Wer hat das schon?
KLEIBERIT gelingt es damit, ein Komplettpaket anzubieten, das sicherlich einzigartig ist - ein international patentiertes Verfahren mit starken Referenzen, eine Demoanlage unter eigener Regie, Kunden-Training unter realen Bedingungen sogar mit kundeneigenem Material.
Die DekoraPUR-Anlage, ausgestattet mit unterschiedlichsten Applikations-Komponenten ist ein wesentlicher Wettbewerbsvorteil. Time-to-market ist heute gefordert. Risikominimierung, Entwicklungsgeschwindigkeit, Überzeugungskraft, Akzeptanz und Vertrauen schaffen sind nur wenige der positiven Effekte, von denen KLEIBERIT, aber auch die Partner und Kunden profitieren.
Erfolgreiche Beispiele finden sich weltweit u. a. bei Kastamonu, PG Bison, Duratex und Tafisa, die in ihren Märkten bestimmend sind. Aber auch das Primeboard von Pfleiderer in Leutkirch hat dort seinen Ursprung.
Historie und Entwicklung der KLEIBERIT HotCoating®-Technologie
Begonnen, so Jens Fandrey, hatte alles im Fußbodenmarkt, speziell mit dem Korkfußboden der Firma LICO/Schweiz. Die erzielte Adhäsion auf dem digital bedruckten Kork-Unterbau, seine Dauerelastizität in sich, als auch seine Strapazierfähigkeit an der Oberfläche, mit einer enormen Abriebfestigkeit von AC 5 lt. Fußbodennorm, überzeugten den bekannten Hersteller und in der Folge auch den zugehörigen Markt.
Der hybride Aufbau des HotCoating besteht quasi aus zwei Schichten, dem Polyurethan in Micro-Emission-Qualität für die Beschichtung und dem passenden UV-Acryllack als Top-Coat. Die reaktive PUR Schicht vernetzt mit Feuchtigkeit, schützt die Oberfläche und den Digitaldruck, die Acrylschicht des Top-Coat härtet mit UV-Strahlung.
Auch die Möbelelemente-Hersteller nutzen seither deren Vorteile.
Sie fragten nach erhöhter Wertschöpfung, Qualität und Produkt-Individualisierung der dekorativen, auch digital bedruckten Platten. Diese sollten in Hochglanz und Supermatt lackiert werden und beste Haftungseigenschaften zwischen Melaminoberfläche und Lackschicht aufweisen, so die Forderungen dieser Industrie. Konventionelle Lacksystem zeigten Probleme bei der Anhaftung auf dem Melamin. Hohe Anlageninvestitionen und teure Primer als Haftvermittler kamen zum Einsatz, aufgetragen auf mehrfach fein geschliffenen Flächen. Aber hohe Ausschussraten durch die Haftungsthematik beim Weiterverarbeiten überzeugten weder die Hersteller noch den Markt.
Wie HotCoating ohne Primer trotzdem eine hohe Haftung erzielt, bleibt ein wohl gehütetes Geheimnis. Die HotCoating Schicht bildet quasi eine Verbund-Einheit mit der Melaminoberfläche, dem Digitaldruck und dem TopCoat und erfüllt daneben alle anderen geforderten Eigenschaften der Platten-Industrie. Selbst eine nachträgliche Poren-Prägung mit bis zu 150 mµ Tiefe, über die vorhandenen KT-Pressen ist ohne Lackrisse möglich.
Ausschlaggebend für den Erfolg und die hohe Markt-Akzeptanz dieser Platten, z.B. des von Pfleiderer hergestellten PRIMEBOARD (siehe Surface Magazin …. ) waren jedoch auch die besonderen Eigenschaften in der Weiterverarbeitung.
In Zeiten von Nullfugen und Laser-Kanten, ist es unumgänglich, dass der Fügefräser an der Plattenkante bzw. der Oberflächenschicht, absolut keine Ausreißer oder Sägezähne erzeugt. Nur so gelingt es, das Kantenband bündig ohne sichtbare Fuge anzufahren. Wenn allerdings die obere Schicht dabei absplittert, ist das teurer Ausschuss. Bei Anlagen mit Losgröße 1 Konzept, beeinflusst die nötige Nacharbeit die Produktivität. Ganz abgesehen von den aktuellen Kostensteigerungen des Platten-Materials, die zusätzlich zu Buche schlagen.
Eine Lösung folgt der nächsten Herausforderung
Die Kompakt-Platte für den Außenbereich war eine solche. Das tolerante HotCoating erlaubt sogar Nacharbeit auf der Baustelle, auch mit weniger idealen Werkzeugen. Die gezeigte Robustheit in der Praxis der Anwendung und die Beständigkeit gegen Wasser, Kälte, Hitze sowie UV-Licht beeindruckt die Kunden.
Das Marktfeedback übertrifft die vorsichtigen Erwartungen von KLEIBERIT bei Weitem.
Auch die Beschichtung von dünnem und biegsamem HPL lag nahe, so Fandrey. Die Biegsamkeit und Flexibilität der Lackschicht war eine Kern-Anforderung, speziell bei CPL.
Die Weiterverarbeitung z.B. im Postforming-Verfahren benötigt die Möglichkeit sehr enge Radien bis runter auf 2-3 mm zu verarbeiten. Nicht jeder Lack oder jede Beschichtung macht das mit, zumindest nicht ohne feine Haar-Risse zu bilden. HotCoating hat es auch hier geschafft, wie der erfolgreiche Einsatz bei Fa. Stylam Industries/Indien deutlich zeigt.
Weitere Innovationen im Blick
Von außen betrachtet überzeugt die intensive Beziehung aller Beteiligter zur Kern-Technologie auch den letzten Zweifler. Jeder Fortschritt, jeder neue Anwendungsfall bringt Erfahrungen und Erkenntnisse, die man aktiv im KLEIBERIT-Team teilt. So gelingt es immer wieder, gemeinsam neue Felder zu erschließen, die vorher unmöglich erschienen und die neue Motivation und Erfolge bringen, so Mansky.
Nur so gelingt es, Themen wie inertes Curing für Hochglanz oder die Excimer-Technik für die Herstellung von supermatten, nahezu reflexionsfreien Oberflächen zu realisieren. Der klare funktionale Aufbau der HotCoating-Schicht, das tiefe Verständnis der beteiligten Experten, die zusätzlichen Erfahrungen der eingebundenen Partnerfirmen, die Offenheit und Bereitschaft das erlangte Wissen zu teilen, um danach neue Lösungen zu finden ist bei KLEIBERIT das Erfolgsgeheimnis, davon ist der Autor überzeugt.
Was lag näher, als auch mit der Rolle-zu-Rolle-Beschichtung weitere neue Kapitel aufzuschlagen. Auf der LIGNA 2017 demonstrierte KLEIBERIT live die erste Anlage mit Inline-Digitaldruck.
Eine Meisterleistung in den Augen der Fachwelt. Stolz berichten Jens Fandrey und Rainer Kampwerth von der aktuellen großen Rolle-zu-Rolle Installation in Florida/USA. Ein Dienstleister für Beschichtungen von bedruckten Papieren und thermoplastischen Folien, hat in eine 1600 mm breite HotCoating-Anlage von Maschinenpartner HUSER investiert.
KLEIBERIT betreut auch diesen Kunden von der Anfrage bis zur Inbetriebnahme mit dem kompletten Paket. Selbst nach erfolgter Inbetriebnahme partizipiert der Kunde von der starken Partnerschaft und dem Innovationsdrang aus Weingarten.
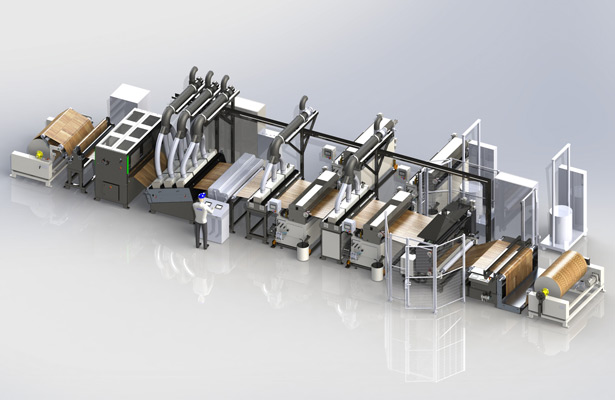
© Huser Maschinenbau GmbH
2009 Inbetriebnahme der ersten Industrieanlage für die Beschichtung von Fußbodenelementen bei LICO / Schweiz
2012 Inbetriebnahme der ersten Rolle-zu-Rolle Industrieanlage für die Beschichtung von Ummantelungsware bei Versatrim / USA
2012 Inbetriebnahme der ersten Industrieanlage für die Hochglanzbeschichtung Holzwerkstoffplatten bei KASTAMONU in Istanbul / Türkei
2013 Inbetriebnahme der ersten HotCoating-Anlage in Südamerika bei DURATEX/ Itapetininga
2015 Entwicklung der Oberflächenprodukte für die Außenanwendung
2017 Inbetriebnahme der zweiten PUR HotCoating Anlage bei KASTAMONU/ Türkei
2017 Entwicklung des Dualcure-HotCoating
2018 Inbetriebnahme der ersten Industrieanlage für die Beschichtung von digital bedruckten faserzementbasierten Fußbodenplatten
2018 Inbetriebnahme der Hochglanz- und Supermattbeschichtungsanlage bei PFLEIDERER in Leutkirch.
2019 Inbetriebnahme der weltweit ersten Industrieanlage für die Beschichtung von 0.80 mm HPL-Schichtstoffplatten
2020 Installation und Inbetriebnahme der ersten High Gloss & Supermatt
2020 Plattenbeschichtungsanlage in Nordamerika bei TAFISA/Canada
2020 Entwicklung und IHD-Zertifizierung brandgehemmter Fassadenbeschichtungsprodukte
2021 Entwicklung neuer HotCoating-Typen mit um 67 % reduzierter Reaktionszeit
2021 Einführung weiterer technischer Eigenschaften wie ME-Qualität, Antibakteriell, Antigraffiti, etc.
2022 PG Bison / Südafrika, nimmt seine zweite HotCoating Anlage in Betrieb
Heute existieren 72 industrielle Beschichtungsanlagen weltweit. In 2022 sind weitere Anlagen für Kunden in Asien und Amerika bestätigt und die Produktionsanlagen befinden sich bei unseren Maschinenpartnern bereits in der Herstellung.
Weiterführende Links
Unternehmensstruktur
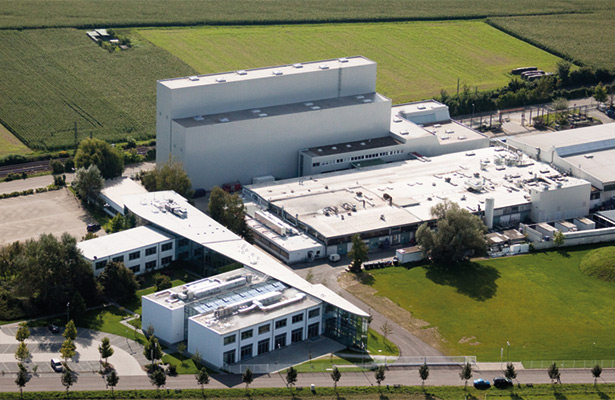
© 2009 Werner Riehm: www.FLY-FOTO.de
Der Kunde ist unsere Orientierung.
KLEIBERIT SE & Co. KG ist ein, auf den Kundendialog ausgerichtetes Unternehmen und entsprechend einfach strukturiert. Es gibt drei Vertriebsbereiche: Den Vertrieb an das Holz verarbeitende Handwerk über den Fachhandel mit den entsprechenden Kundenberatern. Den Vertrieb an die Industrie im Inland und den Vertrieb ins europäische und außereuropäische Ausland mit dem Ingenieursberaternetz direkt vor Ort. Unterstützt werden die Berater durch das Backoffice in Weingarten sowie durch Tochtergesellschaften oder Vertriebsbüros in den wesentlichen Verkaufsregionen.
Die Produktion ist ausschließlich in Weingarten.
International
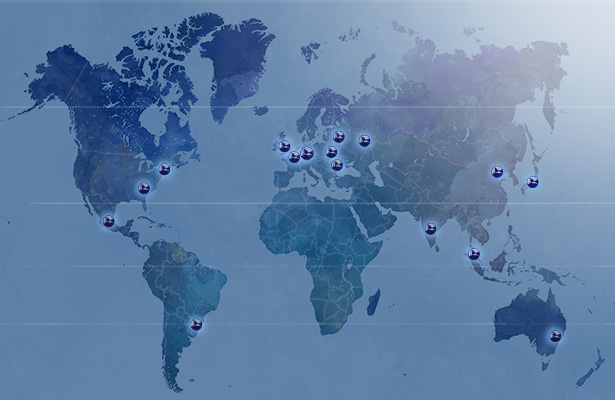
Der Erfolg von KLEIBERIT Klebstoffe ist ein globaler Erfolg.
Kunden aus aller Welt vertrauen uns und setzen auf unsere Qualität und den Service. Deshalb sind wir mit eigenen Gesellschaften und Vertriebsbüros in den wichtigsten Regionen der Welt vertreten.
Unsere Märkte
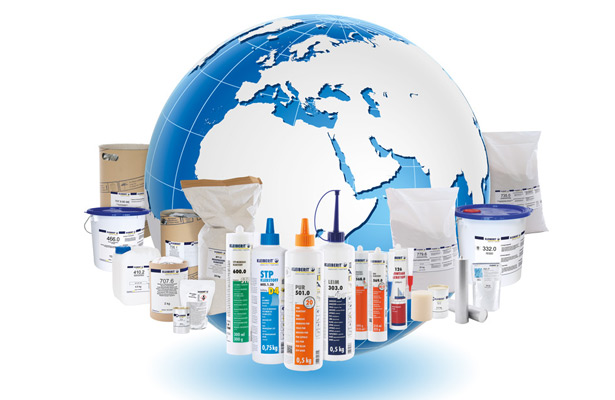
© KLEIBERIT
Viele Anwendungsbereiche setzen auf Verklebungstechnologien von KLEIBERIT.
Hauptmärkte sind das Holz und Kunststoff verarbeitende Handwerk, die Holz- und Möbelindustrie, die Bauindustrie, die Automotive-Industrie, die Textilindustrie sowie die papierverarbeitende Industrie.